產地類別 |
國產 |
價格區間 |
面議 |
應用領域 |
化工,生物產業,石油,制藥/生物制藥,綜合 |
反應器類型 |
攪拌式漿態床或鼓泡塔 |
反應器體積 |
0.1–5 L(實驗室級) |
溫度范圍 |
50–400°C |
壓力范圍 |
1–20 MPa |
攪拌速度 |
100–1500 rpm |
催化劑負載量 |
1–20 wt% |
氣體流量 |
10–1000 mL/min(H?或合成氣) |
液體進料速率 |
0.1–10 mL/min |
加熱方式 |
電加熱套或熔鹽浴 |
氣體分布器 |
燒結金屬或微孔板,確保氣泡均勻 |
分離系統 |
冷凝器+氣液分離器,在線取樣分析 |
漿態床試驗裝置 加氫催化劑評價裝置
我公司主要經營:按要求定制成套反應裝置(加氫反應裝置、精餾裝置、微反評價裝置、固定床評價裝置、流化床評價裝置、催化劑評價裝置等),高低溫循環裝置、高溫循環器、小功率冷水機、顆粒強度測定儀、水熱反應釜等實驗室設備、儀器儀表。
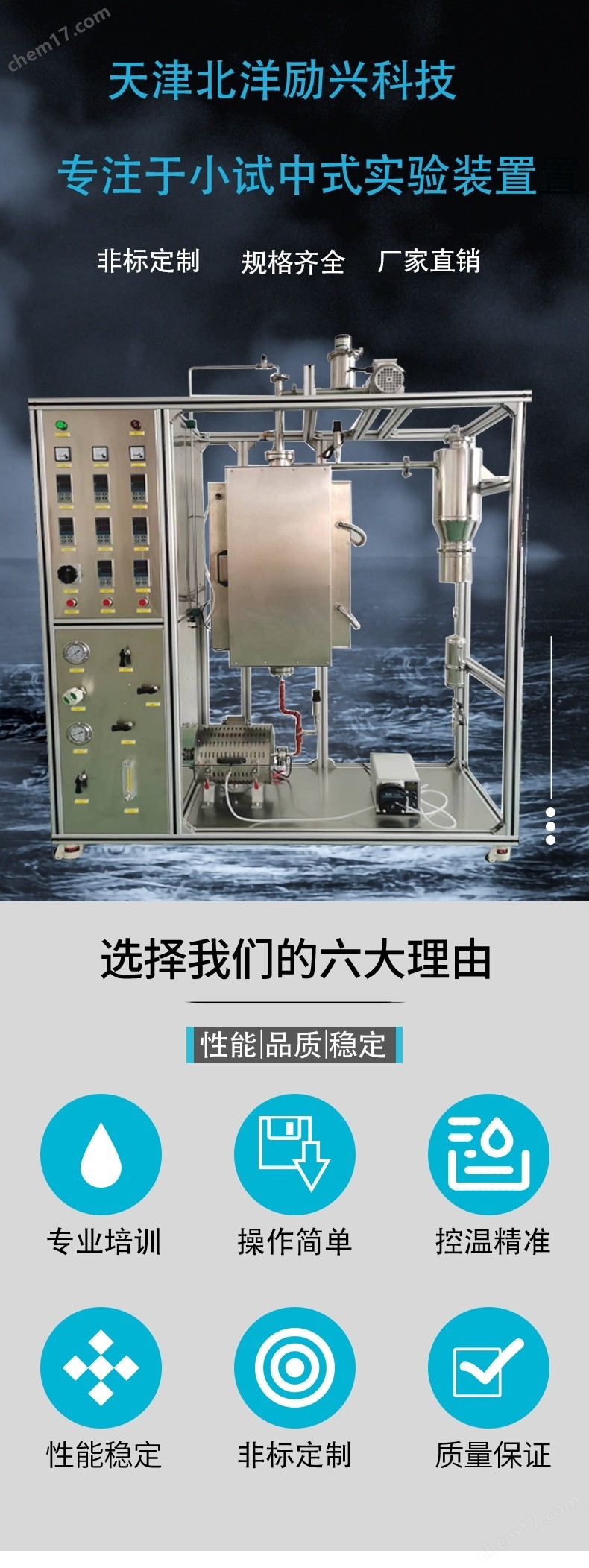
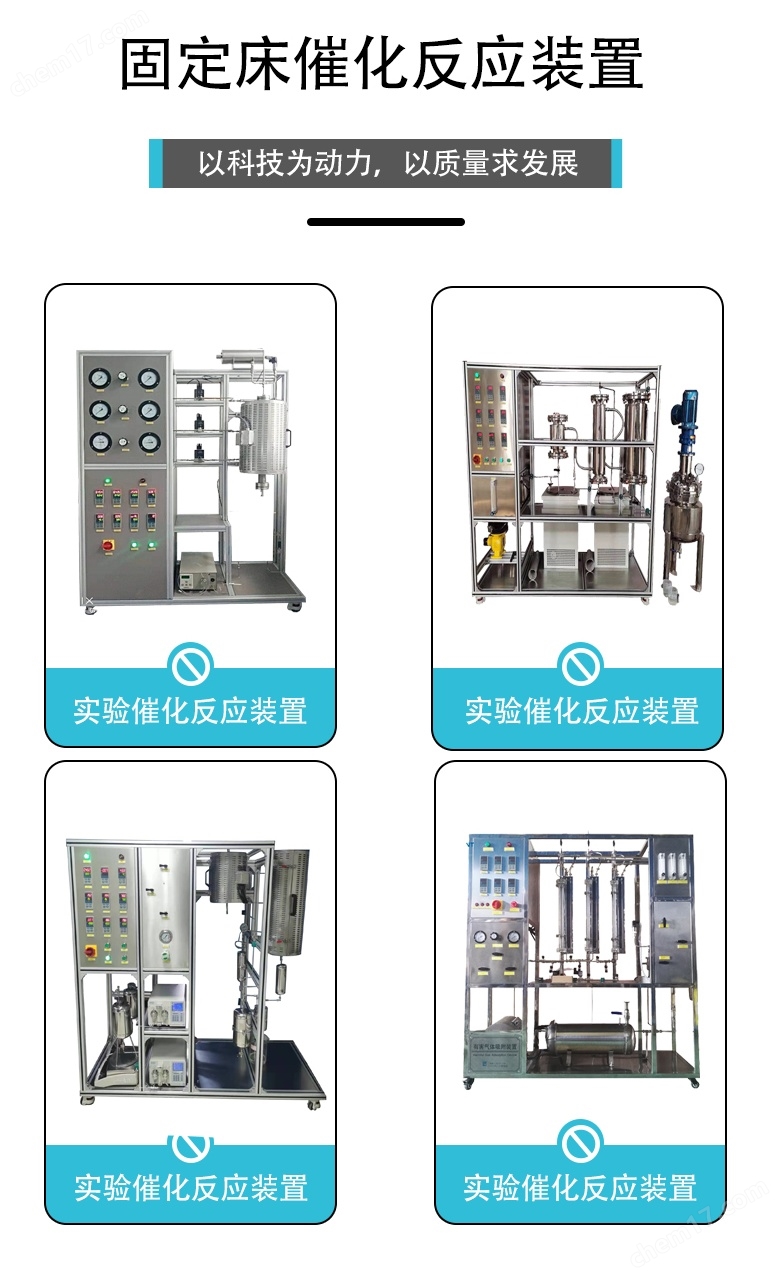
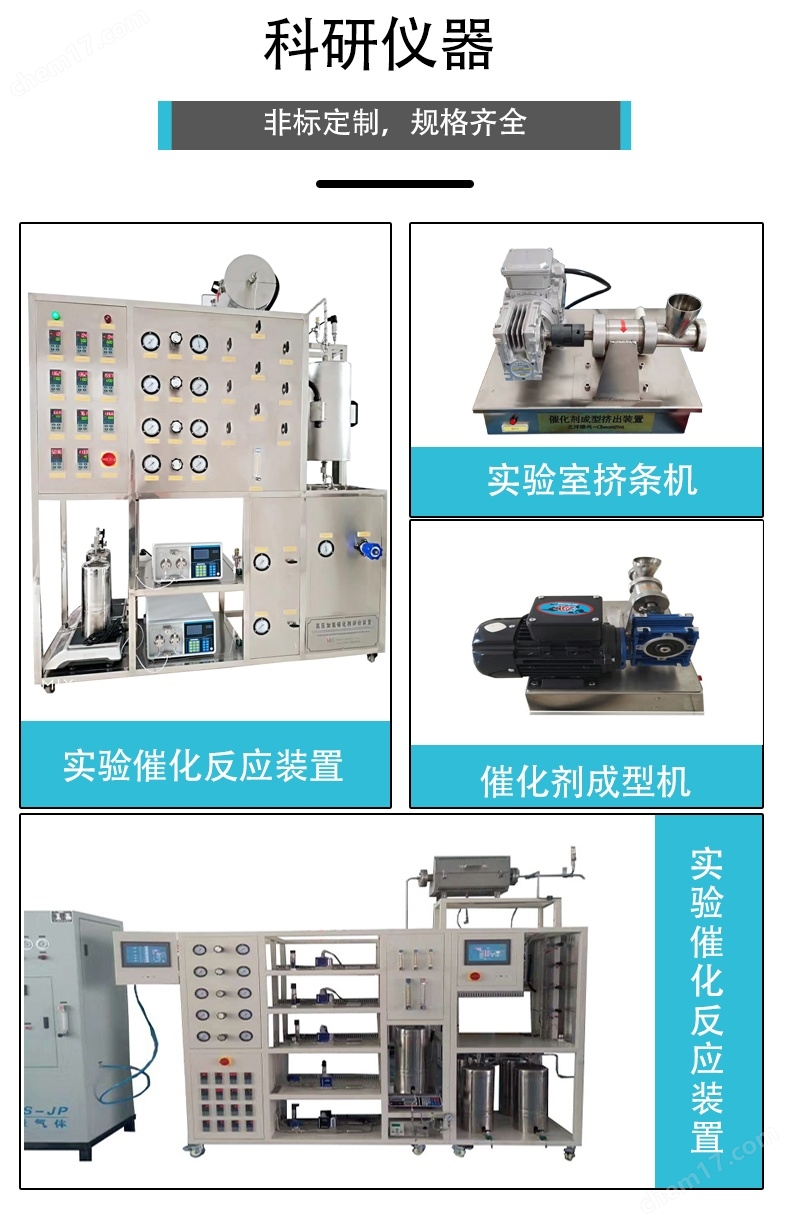

漿態床試驗裝置 加氫催化劑評價裝置
漿態床試驗裝置(Slurry Bed Reactor, SBR)是一種用于氣-液-固三相催化反應的研究設備,廣泛應用于加氫反應、費托合成、生物質液化、重油加工等領域。其核心特點是催化劑以細小顆粒(微米級)懸浮在液體介質中,反應氣體(如H?、CO等)通過鼓泡或攪拌分散,實現高效傳質和反應。1. 漿態床反應器的基本結構漿態床試驗裝置通常由以下主要部分組成:(1) 反應器主體材質:高壓不銹鋼(如316L、哈氏合金)或玻璃(低壓實驗)。結構:攪拌式漿態床:帶機械攪拌(錨式、槳式、渦輪式),適用于高粘度體系。鼓泡塔漿態床:無攪拌,依靠氣體鼓泡實現混合,結構簡單,適合低粘度體系。溫度控制:電加熱套、油浴或外部加熱爐,配合熱電偶/RTD精確控溫。壓力控制:背壓閥+壓力傳感器,維持穩定反應壓力。(2) 進料系統液體進料:高壓微量泵(如HPLC泵)控制液體(油、溶劑等)流速。氣體進料:質量流量控制器(MFC)調節H?、CO、N?等氣體流量。催化劑進料:可預先混合在液體中,或通過特殊進料器連續加入。(3) 攪拌/氣體分布系統機械攪拌:轉速可調(100–2000 rpm),確保催化劑均勻懸浮。氣體分布器:燒結金屬或多孔板,使氣體形成微小氣泡,提高氣液接觸面積。(4) 分離與產物收集氣液分離:冷凝器+氣液分離罐,分離未反應氣體和液體產物。固液分離:過濾器或離心機回收催化劑(可循環使用)。在線分析:GC(氣相色譜)、MS(質譜)等實時監測反應產物。2. 漿態床反應器的特點? 優點傳質效率高:催化劑顆粒懸浮在液體中,氣-液-固接觸充分,適合高粘度或固體含量高的反應體系(如煤液化、重油加氫)。溫度均勻:攪拌或鼓泡使反應體系溫度分布更均勻,避免局部過熱。催化劑利用率高:細小催化劑顆粒提供高比表面積,反應活性高。靈活性強:可適應間歇或連續操作,催化劑更換方便。? 局限性催化劑分離困難:反應后需過濾或離心回收催化劑,可能造成損失。攪拌能耗高:高粘度體系需要較強攪拌,增加能耗。放大挑戰:工業放大時需解決固體懸浮、氣泡分布等問題。3. 典型應用領域應用領域反應示例適用原因重油/渣油加氫重油脫硫、脫氮高粘度原料,需高效催化劑接觸煤/生物質液化煤直接液化(DCL)固體原料需懸浮在溶劑中反應費托合成CO + H? → 烴類(燃料、蠟)需要良好氣液傳質和溫度控制精細化工硝基化合物加氫還原高選擇性,避免催化劑堵塞4. 實驗室級 vs. 工業級漿態床參數實驗室級工業級反應器體積0.1–10 L1–100 m3操作壓力1–10 MPa5–30 MPa催化劑回收過濾/離心連續分離(如旋流器、沉降器)攪拌方式機械攪拌或鼓泡大型攪拌器或氣體循環系統5. 關鍵設計考慮因素催化劑選擇:粒徑(通常1–100 μm)、抗磨損性、懸浮穩定性。氣液傳質優化:氣泡大小、氣體流速、攪拌強度。反應工程控制:溫度、壓力、停留時間、催化劑濃度。安全措施:防爆設計、氫氣泄漏檢測、緊急泄壓系統。總結漿態床試驗裝置是研究三相催化反應的重要工具,特別適用于高粘度、含固體或需要高效傳質的反應體系。實驗室裝置通常采用攪拌式或鼓泡塔設計,而工業裝置需解決催化劑分離、放大效應等問題。在能源化工(煤/生物質轉化)、石油 refining、精細化工等領域具有廣泛應用。
漿態床試驗裝置(Slurry Bed Reactor, SBR)是一種用于氣-液-固三相催化反應的研究設備,廣泛應用于加氫反應、費托合成、生物質液化、重油加工等領域。其核心特點是催化劑以細小顆粒(微米級)懸浮在液體介質中,反應氣體(如H?、CO等)通過鼓泡或攪拌分散,實現高效傳質和反應。
1. 漿態床反應器的基本結構
漿態床試驗裝置通常由以下主要部分組成:
(1) 反應器主體
(2) 進料系統
液體進料:高壓微量泵(如HPLC泵)控制液體(油、溶劑等)流速。
氣體進料:質量流量控制器(MFC)調節H?、CO、N?等氣體流量。
催化劑進料:可預先混合在液體中,或通過特殊進料器連續加入。
(3) 攪拌/氣體分布系統
(4) 分離與產物收集
氣液分離:冷凝器+氣液分離罐,分離未反應氣體和液體產物。
固液分離:過濾器或離心機回收催化劑(可循環使用)。
在線分析:GC(氣相色譜)、MS(質譜)等實時監測反應產物。
2. 漿態床反應器的特點
? 優點
傳質效率高:催化劑顆粒懸浮在液體中,氣-液-固接觸充分,適合高粘度或固體含量高的反應體系(如煤液化、重油加氫)。
溫度均勻:攪拌或鼓泡使反應體系溫度分布更均勻,避免局部過熱。
催化劑利用率高:細小催化劑顆粒提供高比表面積,反應活性高。
靈活性強:可適應間歇或連續操作,催化劑更換方便。
? 局限性
催化劑分離困難:反應后需過濾或離心回收催化劑,可能造成損失。
攪拌能耗高:高粘度體系需要較強攪拌,增加能耗。
放大挑戰:工業放大時需解決固體懸浮、氣泡分布等問題。
3. 典型應用領域
應用領域 | 反應示例 | 適用原因 |
---|
重油/渣油加氫 | 重油脫硫、脫氮 | 高粘度原料,需高效催化劑接觸 |
煤/生物質液化 | 煤直接液化(DCL) | 固體原料需懸浮在溶劑中反應 |
費托合成 | CO + H? → 烴類(燃料、蠟) | 需要良好氣液傳質和溫度控制 |
精細化工 | 硝基化合物加氫還原 | 高選擇性,避免催化劑堵塞 |
4. 實驗室級 vs. 工業級漿態床
參數 | 實驗室級 | 工業級 |
---|
反應器體積 | 0.1–10 L | 1–100 m3 |
操作壓力 | 1–10 MPa | 5–30 MPa |
催化劑回收 | 過濾/離心 | 連續分離(如旋流器、沉降器) |
攪拌方式 | 機械攪拌或鼓泡 | 大型攪拌器或氣體循環系統 |
5. 關鍵設計考慮因素
催化劑選擇:粒徑(通常1–100 μm)、抗磨損性、懸浮穩定性。
氣液傳質優化:氣泡大小、氣體流速、攪拌強度。
反應工程控制:溫度、壓力、停留時間、催化劑濃度。
安全措施:防爆設計、氫氣泄漏檢測、緊急泄壓系統。
漿態床試驗裝置 加氫催化劑評價裝置
漿態床試驗裝置是研究三相催化反應的重要工具,特別適用于高粘度、含固體或需要高效傳質的反應體系。實驗室裝置通常采用攪拌式或鼓泡塔設計,而工業裝置需解決催化劑分離、放大效應等問題。在能源化工(煤/生物質轉化)、石油 refining、精細化工等領域具有廣泛應用。
漿態床試驗裝置(Slurry Bed Reactor, SBR)是一種用于氣-液-固三相催化反應的研究設備,廣泛應用于加氫反應、費托合成、生物質液化、重油加工等領域。其核心特點是催化劑以細小顆粒(微米級)懸浮在液體介質中,反應氣體(如H?、CO等)通過鼓泡或攪拌分散,實現高效傳質和反應。1. 漿態床反應器的基本結構漿態床試驗裝置通常由以下主要部分組成:(1) 反應器主體材質:高壓不銹鋼(如316L、哈氏合金)或玻璃(低壓實驗)。結構:攪拌式漿態床:帶機械攪拌(錨式、槳式、渦輪式),適用于高粘度體系。鼓泡塔漿態床:無攪拌,依靠氣體鼓泡實現混合,結構簡單,適合低粘度體系。溫度控制:電加熱套、油浴或外部加熱爐,配合熱電偶/RTD精確控溫。壓力控制:背壓閥+壓力傳感器,維持穩定反應壓力。(2) 進料系統液體進料:高壓微量泵(如HPLC泵)控制液體(油、溶劑等)流速。氣體進料:質量流量控制器(MFC)調節H?、CO、N?等氣體流量。催化劑進料:可預先混合在液體中,或通過特殊進料器連續加入。(3) 攪拌/氣體分布系統機械攪拌:轉速可調(100–2000 rpm),確保催化劑均勻懸浮。氣體分布器:燒結金屬或多孔板,使氣體形成微小氣泡,提高氣液接觸面積。(4) 分離與產物收集氣液分離:冷凝器+氣液分離罐,分離未反應氣體和液體產物。固液分離:過濾器或離心機回收催化劑(可循環使用)。在線分析:GC(氣相色譜)、MS(質譜)等實時監測反應產物。2. 漿態床反應器的特點? 優點傳質效率高:催化劑顆粒懸浮在液體中,氣-液-固接觸充分,適合高粘度或固體含量高的反應體系(如煤液化、重油加氫)。溫度均勻:攪拌或鼓泡使反應體系溫度分布更均勻,避免局部過熱。催化劑利用率高:細小催化劑顆粒提供高比表面積,反應活性高。靈活性強:可適應間歇或連續操作,催化劑更換方便。? 局限性催化劑分離困難:反應后需過濾或離心回收催化劑,可能造成損失。攪拌能耗高:高粘度體系需要較強攪拌,增加能耗。放大挑戰:工業放大時需解決固體懸浮、氣泡分布等問題。3. 典型應用領域應用領域反應示例適用原因重油/渣油加氫重油脫硫、脫氮高粘度原料,需高效催化劑接觸煤/生物質液化煤直接液化(DCL)固體原料需懸浮在溶劑中反應費托合成CO + H? → 烴類(燃料、蠟)需要良好氣液傳質和溫度控制精細化工硝基化合物加氫還原高選擇性,避免催化劑堵塞4. 實驗室級 vs. 工業級漿態床參數實驗室級工業級反應器體積0.1–10 L1–100 m3操作壓力1–10 MPa5–30 MPa催化劑回收過濾/離心連續分離(如旋流器、沉降器)攪拌方式機械攪拌或鼓泡大型攪拌器或氣體循環系統5. 關鍵設計考慮因素催化劑選擇:粒徑(通常1–100 μm)、抗磨損性、懸浮穩定性。氣液傳質優化:氣泡大小、氣體流速、攪拌強度。反應工程控制:溫度、壓力、停留時間、催化劑濃度。安全措施:防爆設計、氫氣泄漏檢測、緊急泄壓系統。總結漿態床試驗裝置是研究三相催化反應的重要工具,特別適用于高粘度、含固體或需要高效傳質的反應體系。實驗室裝置通常采用攪拌式或鼓泡塔設計,而工業裝置需解決催化劑分離、放大效應等問題。在能源化工(煤/生物質轉化)、石油 refining、精細化工等領域具有廣泛應用。